The SynqNet Motion Controller
Open, powerful, and economical PC based SynqNet soft motion controller for OEM machine builders.
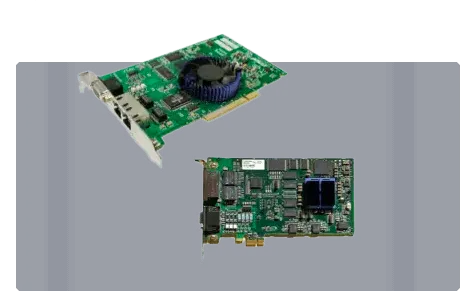
Upgrade Path
Learn how to migrate from the ZMP/QMP SynqNet to the RMP EtherCAT® Motion Controller
Key Benefits
QMP / ZMP (PCIe or PCI)
No RTOS required, yet still achieves superior real-time, synchronous network performance (up to 48 KHz servo update rate, <100ns jitter)
The ZMP/QMP motion controller card is a pre-installed package with our Standalone IPC’s
(replace a failed node without stopping machine)
Controller firmware is customizable using MechaWare (MATLAB) which allows implementation of advanced custom control algorithms.
Supports up to 64 nodes with 64 axes.
Featuring a 64-bit PowerPC processor ranging from 266MHz up to a 1.2 GHz
Architecture
Interrelationship of physical components
- Motion firmware runs on dedicated Power PC processor on controller card for extremely high deterministic performance.
- Communicates via SynqNet to devices on the network
- User’s application software and diagnostic tools to run in Windows
- RapidCode API Libraries bridge between windows applications and the motion firmware
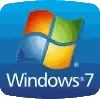
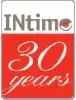
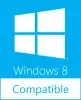
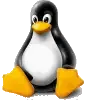
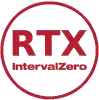
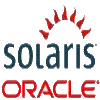
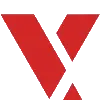
Software
Powerful and intuitive tools to create motion applications and speed up development
RapidCode API
RapidCode is a powerful and intuitive Application Programming Interface (API) that allows developers to quickly create machine control applications in C++, C#, or VB.Net. The API is broken down into simple classes — Controller, Axis and Multiaxis and IO.
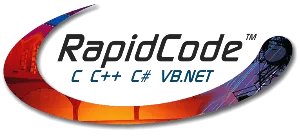
RapidSetup
RapidSetup is an easy to use utility for configuration, homing, tuning, commanding motion, and troubleshooting. The always visible tree view, shows the real-time status and topology for all the nodes on the network allowing for simpler navigation and configuration of the system. I/O status is clearly visible as well as motion parameters such as command position, actual position, errors, and faults.
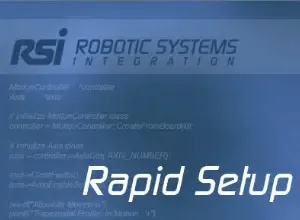
MotionScope
MotionScope plots and traces I/O signal data from any address on the motion controller. It is similar in its presentation to an oscilloscope, and is an exceptional utility for developing and troubleshooting motion control systems.
Bode Tool
The Bode Tool is a utility that makes it easy to get frequency domain data from your system. The Bode Tool makes it easy to get the data a controls engineer needs to set up and tune the control system properly.
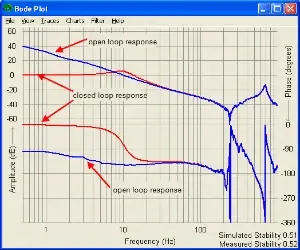
Mechaware
MechaWare enables software and mechanical engineers to design, test, and modify custom motion control algorithms quickly and easily.
MechaWare leverages MATLAB®/Simulink® to integrate mechanical systems and control software design resulting in faster design cycles and superior motion system performance.
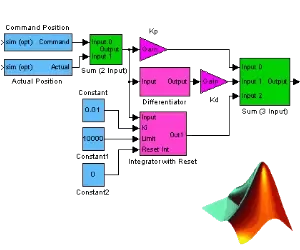
VM3
The VM3 utility allows you to view and alter data stored in memory in either the RMP, QMP, or ZMP controllers. The VM3 is especially useful for locating memory addresses for plotting custom signals in MotionScope. When using VM3 to alter data on motion controllers, exercise extreme caution at all times.
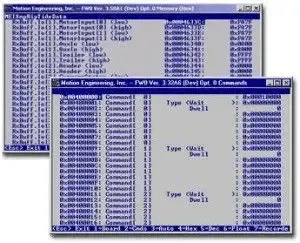
Controller Features
Our SynqNet Controller offers many motion and IO features
Execute drive level autotuning while in position mode from the API or optimize machine performance with frequency response tuning tools while in torque mode.
Stream of raw data points which represent an entire motion profile. PT, PVT, PVAJT motion streaming types are available
Execute pre-defined or custom homing routines.
Moves from current command position to a new position (Trapezoidal, Move S-Curve)
Maintain constant velocity between points. An example is Conveyor axis. The ability to gradually ramp up or ramp down the velocity.
Configure input comparisons to trigger outputs or other events. Conditions are monitored at the firmware level. When the condition is true, the configured response is generated.
Geometric path motion allows complex 2D and 3D paths to be specified using simple geometric elements (arcs and lines).
The position of a slave axis is mathematically linked to the position of a master axis. Create a table and start with camming.
Provides a mechanism to collect and buffer any data in memory. The data is later polled via interrupt-based events.
Multiple control schemes are available including algorithms where separate PID’s control the linear and Yaw Axis.
Provide the ability to interrupt the host at a specified frequency, where the frequency is a multiple of the controller’s sample rate
It is possible to seamlessly replace a drive on a machine without interrupting motion on other axes.
Configure an axis’ commanded position to be geared off of another axis.
Latch the position counters in the FPGA and are read directly by the controller. The ability to latch axis’ position based on one or more source input triggers.
Add cable break, drive, or motor fault warning/messages directly into software
Enable secondary feedback
Applications
Controller applications and industry examples
Cutting Machines
- Path Motion – Create shapes quickly by adding Arcs and Line segments
- Electronic gearing to synchronize two axes on a gantry
- Frequency response tuning tools to optimize system bandwidth and stability
- RapidBode tracks bandwidth and stability over time on machines of varying sizes
- High speed digital I/O trigger and capture
- Intelligent Machine Status/diagnostics
- Leather, Fabric, Carbon Fiber, Plastic, Rubber, etc.
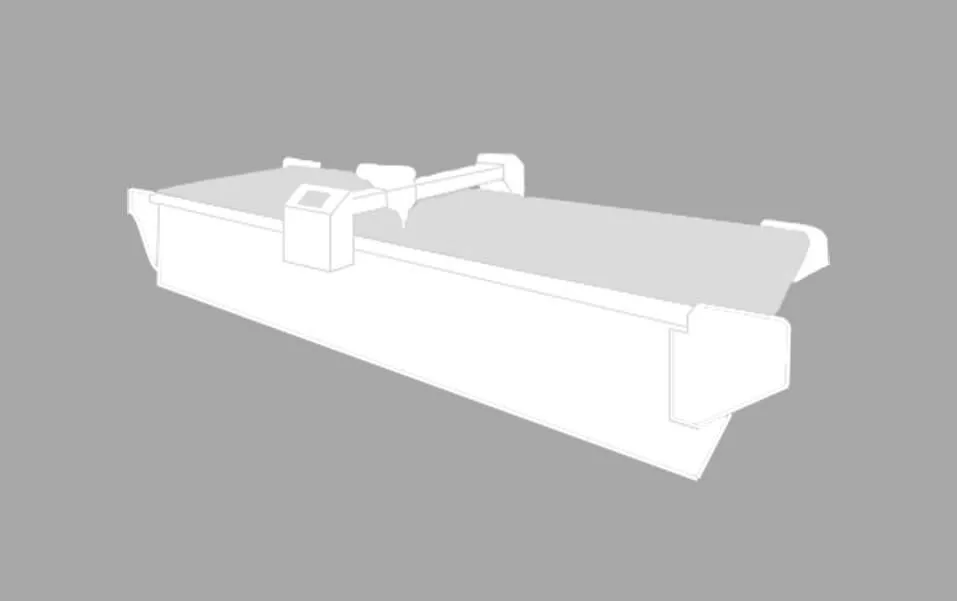
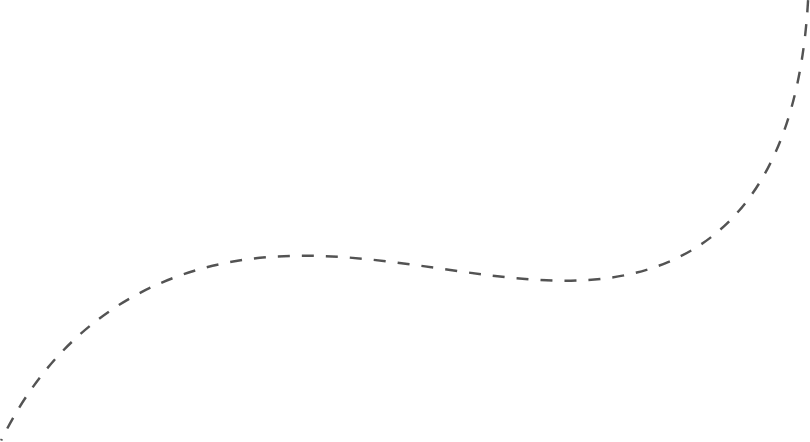
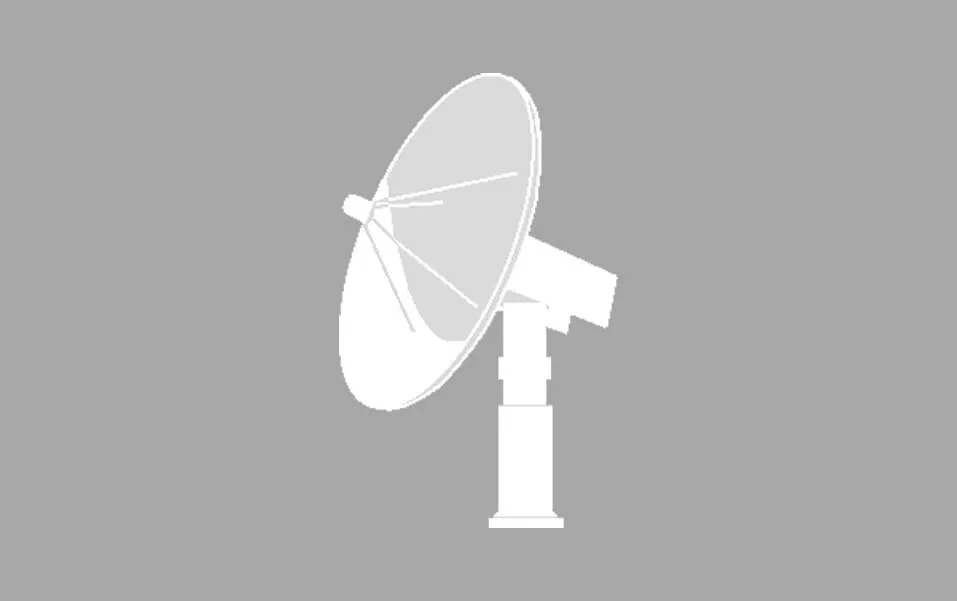
Aerospace & Defense
- Ability to create customized dual motor control algorithms which help improve accuracy, repeatability, performance, and stability by eliminating backlash
- Latency times are reduced dramatically by using our RapidCode for INtime (API that runs on INtime Real-Time Operating System)
- Custom device drivers support multiple operating systems such as Vxworks, QNX, Linux, and others
- Modification of motion trajectories on the fly
- Frequency response tuning tools to optimize system bandwidth
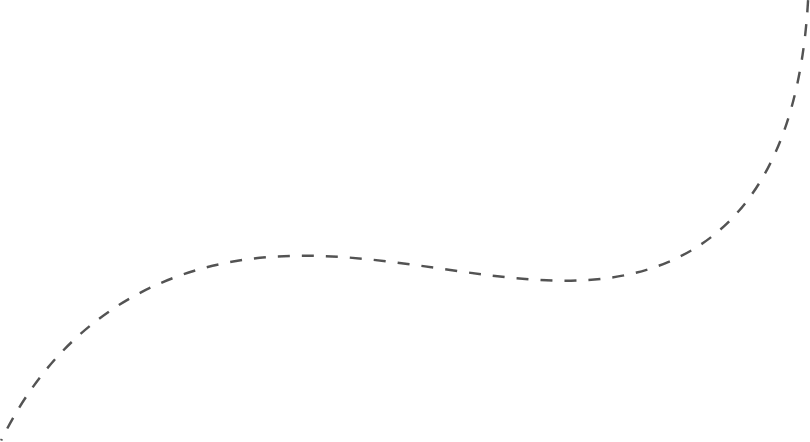
Solar
- High axis counts
- Synchronized multi-axis streaming motion
- High speed digital I/O trigger and capture
- High performance precise motion
- Motion Programming in C/C++/C#/VB.NET using the powerful RapidCode programming API
- Frequency response tuning tools to optimize system bandwidth and stability
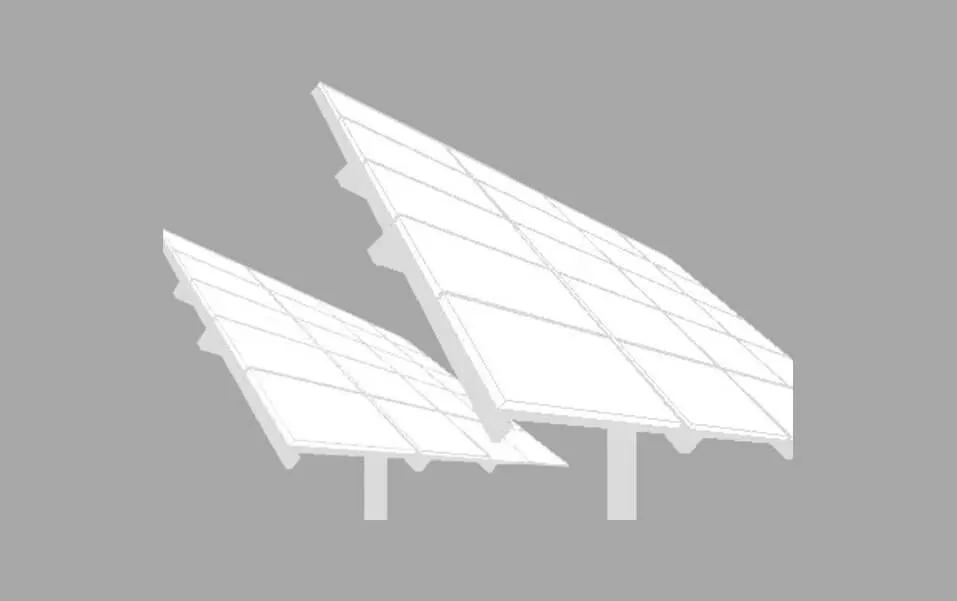
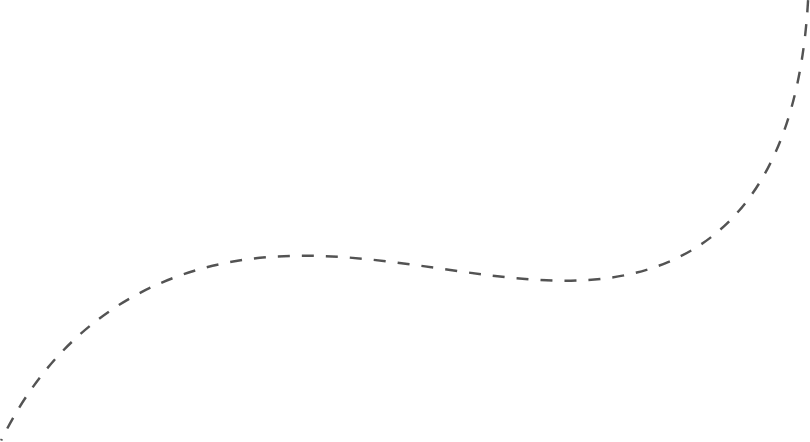
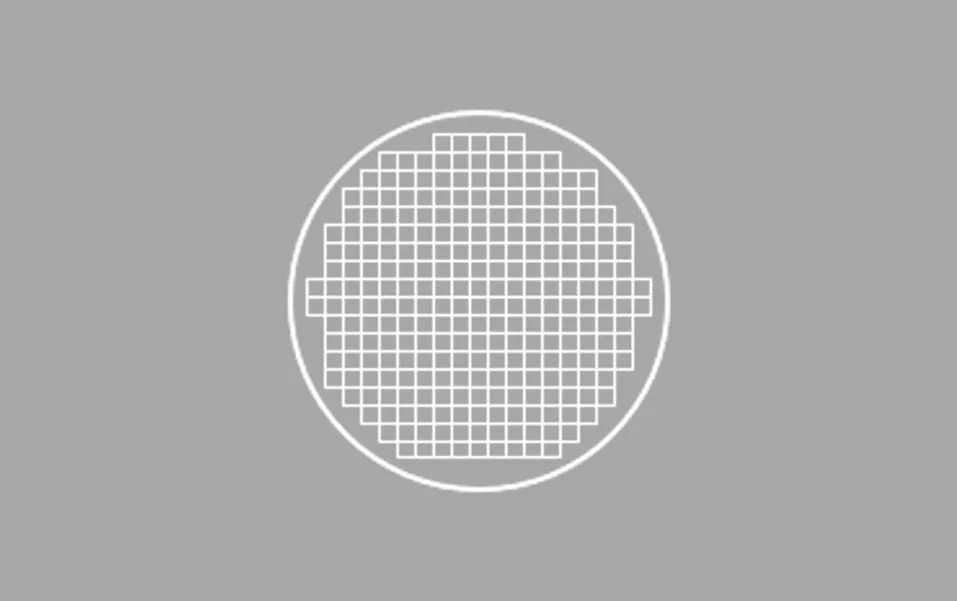
Semiconductor
- Synchronized multi-axis streaming motion
- High speed digital I/O trigger and capture
- High performance precise motion
- Secondary feedback easily added to control loop
- High axis counts
- Frequency response tuning tools to optimize system bandwidth and stability
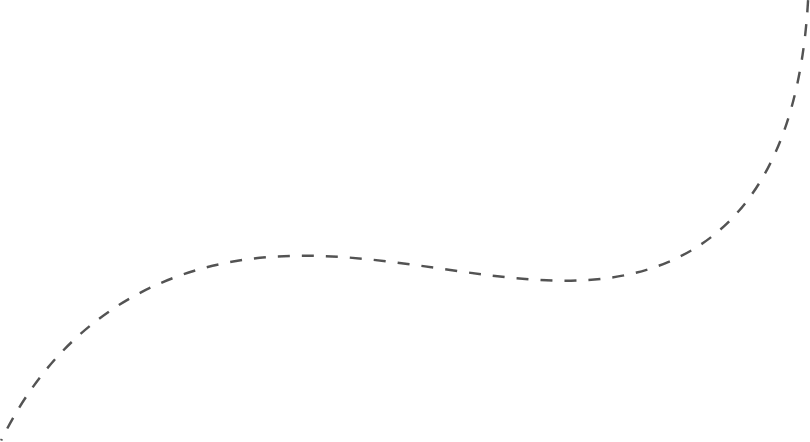
Medical
- Synchronized multi-axis streaming motion
- Ability to embed kinematics in firmware
- Dual safety controller and servo drives
- Native torque mode useful for applying force
- Configure input comparisons to trigger outputs or other events, monitored at the firmware level
- Frequency response tuning tools to optimize system bandwidth and stability
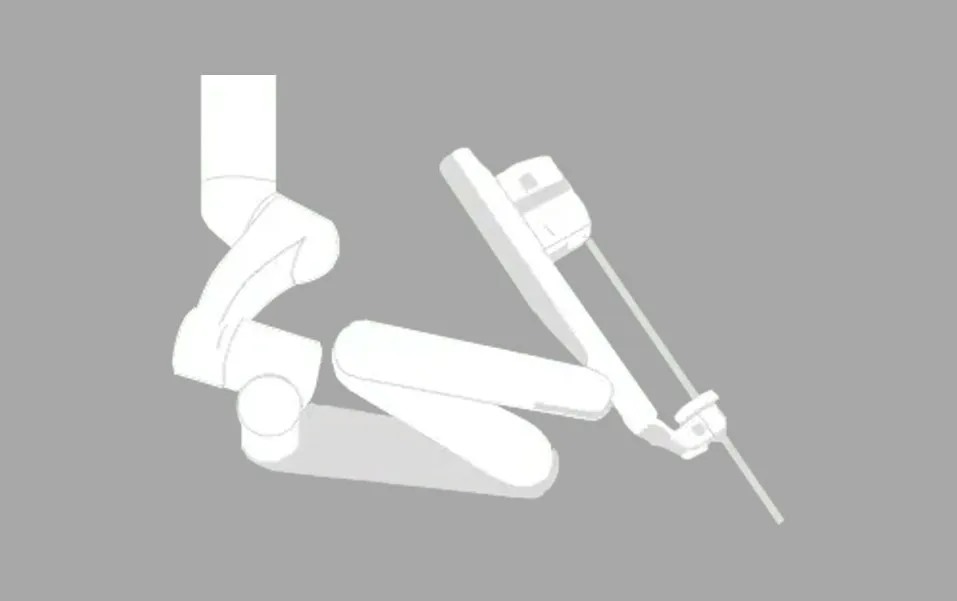
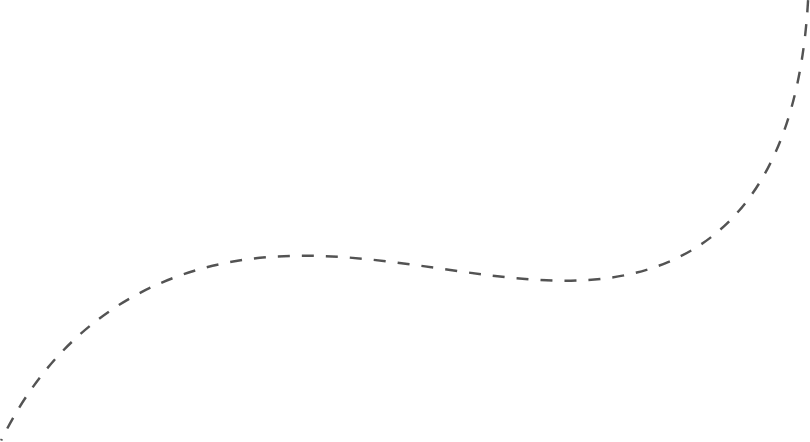
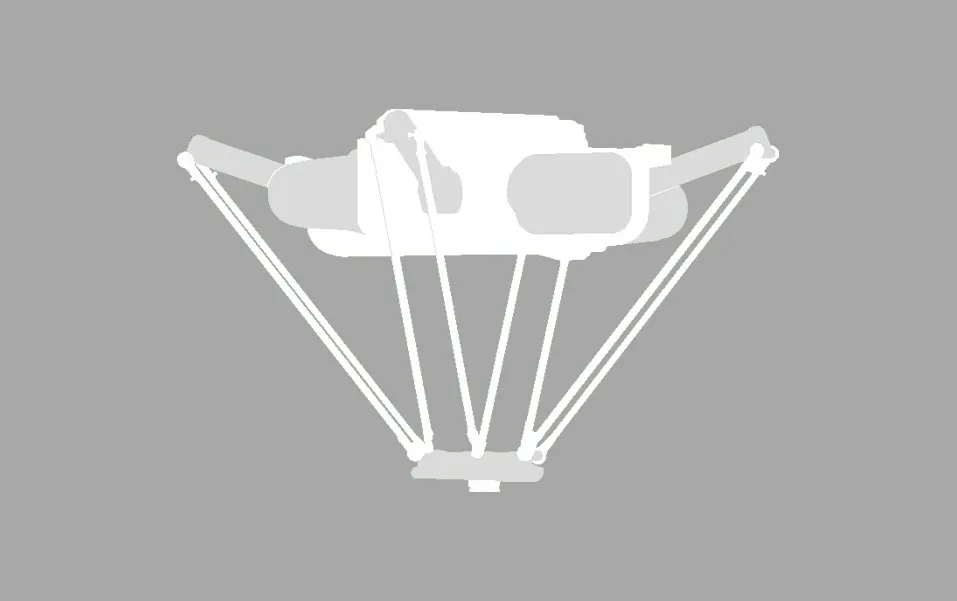
Delta Robot
- Ability to embed kinematics in firmware
- Synchronized multi-axis streaming motion
- High speed digital I/O trigger and capture
- Motion Programming in C/C++/C#/VB.NET using the powerful RapidCode programming API
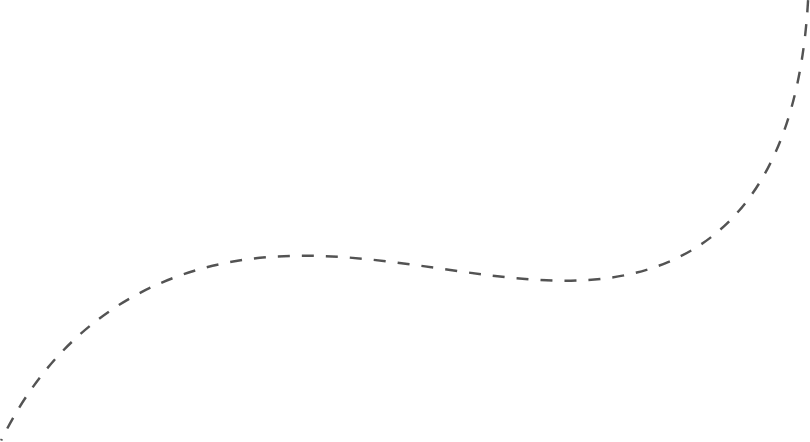
Servo Press
- Load cell / force transducer feedback into servo loop
- Ability to switch between Position and Force control modes
- Real-Time Data recording built into motion firmware
- Economical control solution
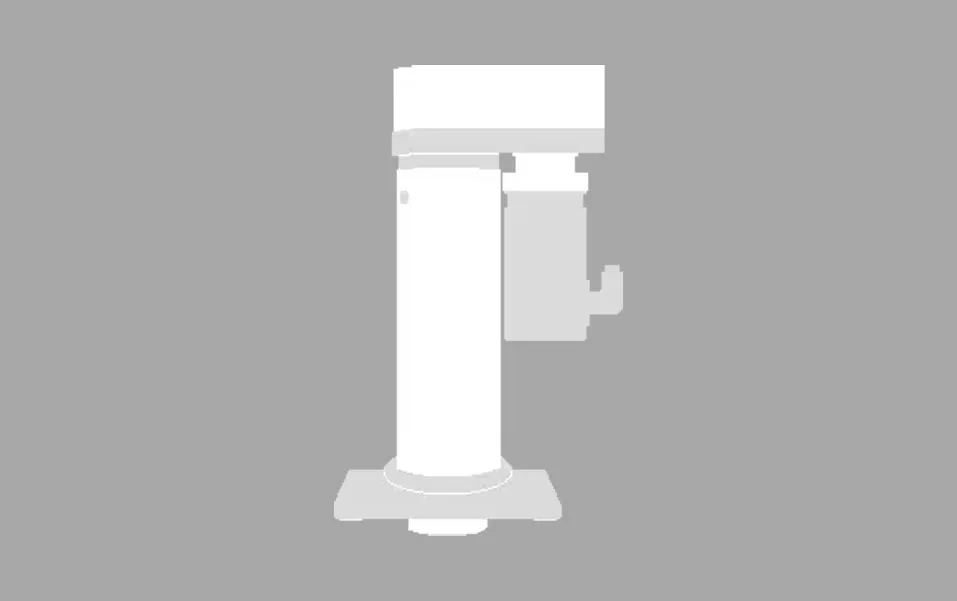
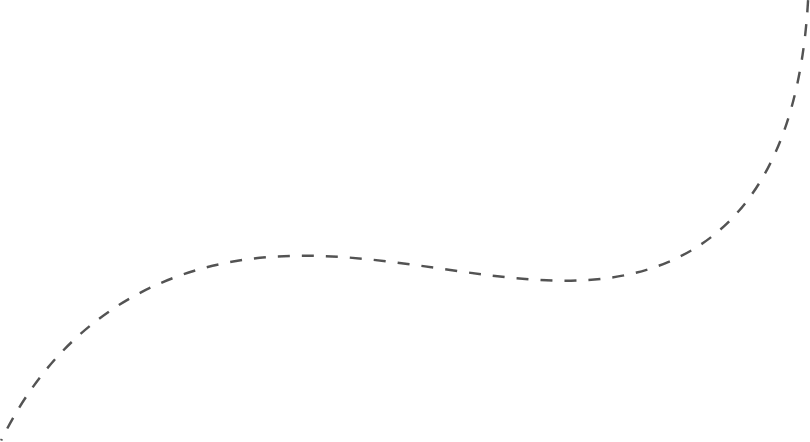

Packaging
- High speed digital I/O trigger and capture
- Configure input comparisons to trigger outputs or other events, monitored at the firmware level
- Mathematically link the position of a slave axis to the position of a master axis using by defining a relationship table called Camming
- Ability to interrupt the host at a specified frequency, where the frequency is a multiple of the controller’s sample rate
start developing today!
1000+ customers have already automated with help of our products and team