ZMP/QMP to RMP
Learn how to migrate from the ZMP/QMP SynqNet to the RMP EtherCAT® Motion Controller
Overview
See why migrating to the RMP EtherCAT® Motion Controller will benefit you
With the obsolescence of ZMP and QMP SynqNet cards, OEMs can migrate to the RMP EtherCAT® Soft Motion Controller utilizing the current source code written using the MPI API. The RMP EtherCAT® Motion Controller uses the same motion firmware as the ZMP and QMP SynqNet cards. Most of the software tools remain intact. Converting to RMP significantly reduces the learning curve and enables OEMs to leverage years of development.
Some advantages of migrating to the RMP EtherCAT®:
1. Hardware
The RMP® is a software-based motion controller and runs on standard Industrial PC hardware. Hence, no need to worry about components or controller hardware going obsolete.
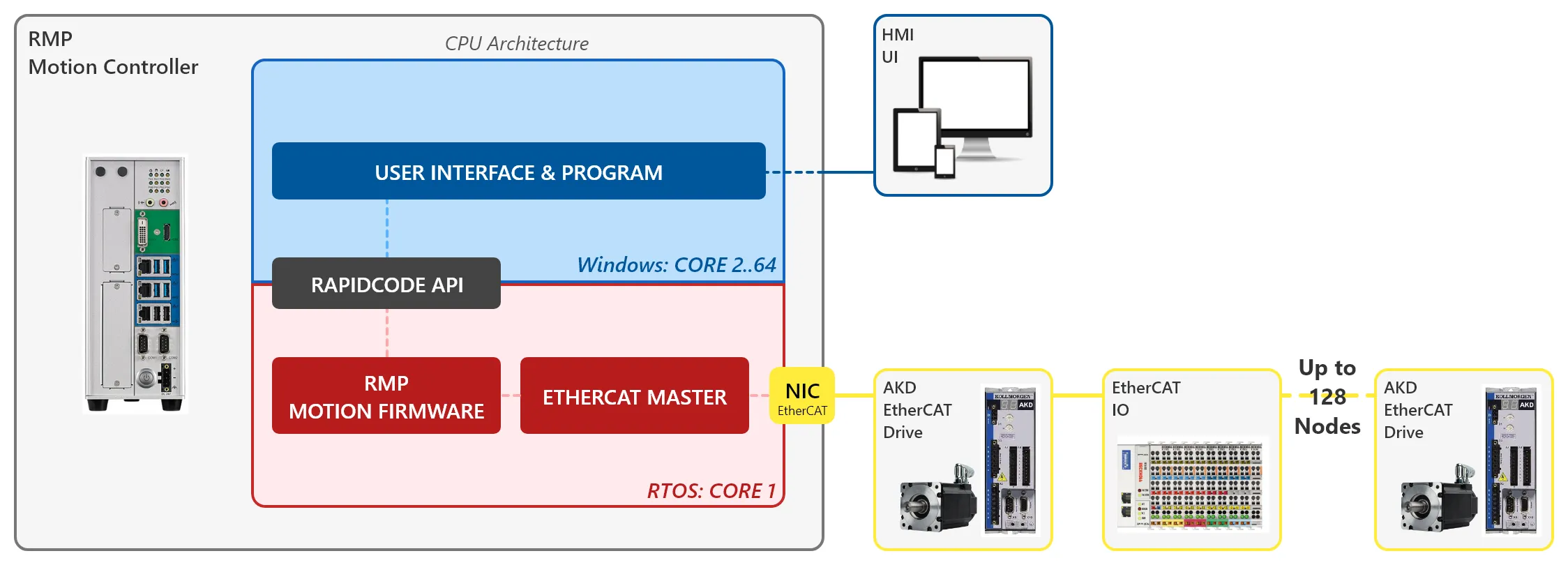
2. Performance
Most OEMs run RMP with drives in the position loop. Closing the position loop in the EtherCAT® drive is better as the drive's internal interpolation sample rate is high. SynqNet closes the torque loop in the controller. Therefore, with high axis counts, the SynqNet controller sample rate has to be set lower which leads to lower system performance when closing the motor's feedback loop.
3. Features
The RMP motion firmware is the same as ZMP/QMP SynqNet™ cards. Hence, OEMs can utilize the same tested and proven feature set.
4. Software API
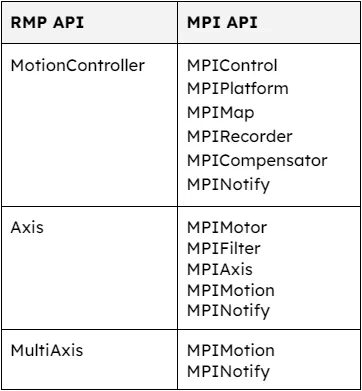
The RMP EtherCAT® supports MPI API (C language). Current SynqNet™ OEMs can leverage MPI and utilize a modern and popular communications layer (EtherCAT®) with minimal effort.
Most of the machine’s source code will remain untouched. The primary changes from migrating to the RMP EtherCAT® will be made to Network Initialization and Homing. Here on the right is a list of supported MPI objects using the RMP EtherCAT® motion controller.
A machine's software comprises tens of thousands of lines of code, and a significant portion of the code relates to motion and IO. This code is critical because implementing the code requires actual hardware testing and synchronizing all the various pieces. Once a machine goes into production, the necessary motion and IO code are not altered, whereas front-end UI-related code is often enhanced as new features are added.
Rewriting all the motion and IO code for a machine typically takes 12-18 months. It is time-consuming to understand the features/tools of a new motion controller and how the various function calls are utilized.
RMP’s RapidCode also supports other languages such as C++, C#, and VB. NET. For non-Windows programmers, utilizing RapidCodeRemote gRPC services enables OEMs to use many more languages such as Python, Java, Ruby, Dart, etc.
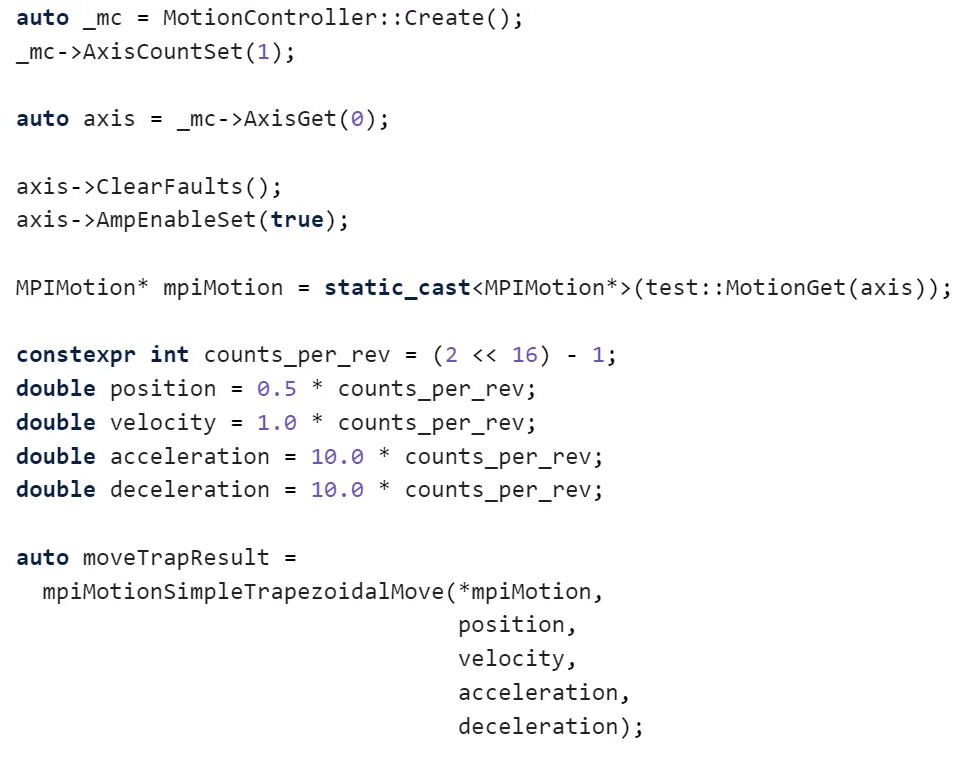
5. Software Tools
Valuable tools such as MotionScope and BodeTool remain unchanged, lessening any learning curve for the engineers and technicians.
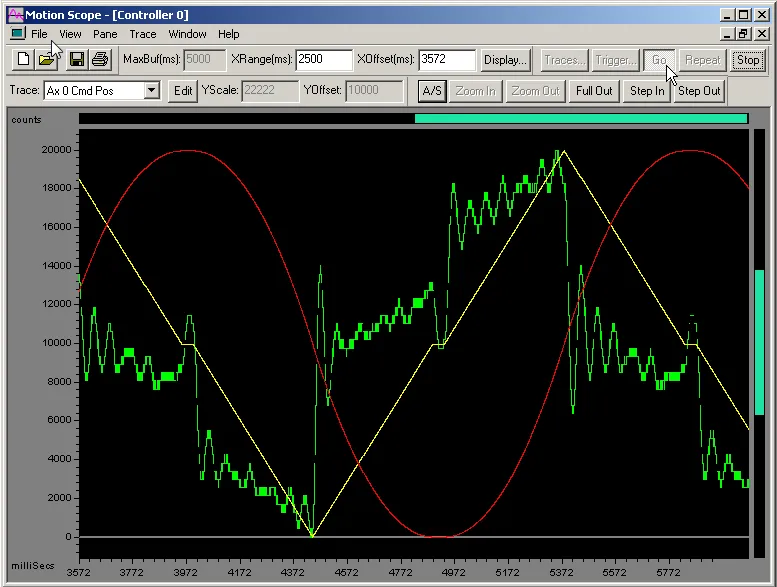
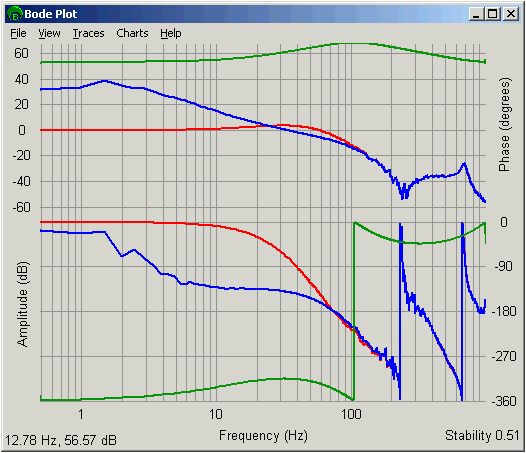
Improved MotionConsole
RapidSetup was designed to organize various aspects of the MotionConsole better. RapidSetup has a clean tree view format making it easy to view axes, especially when high axis counts are involved. RapidSetup also allows engineers to rename various axes and IOs making it easier to control the multiple products in a machine.
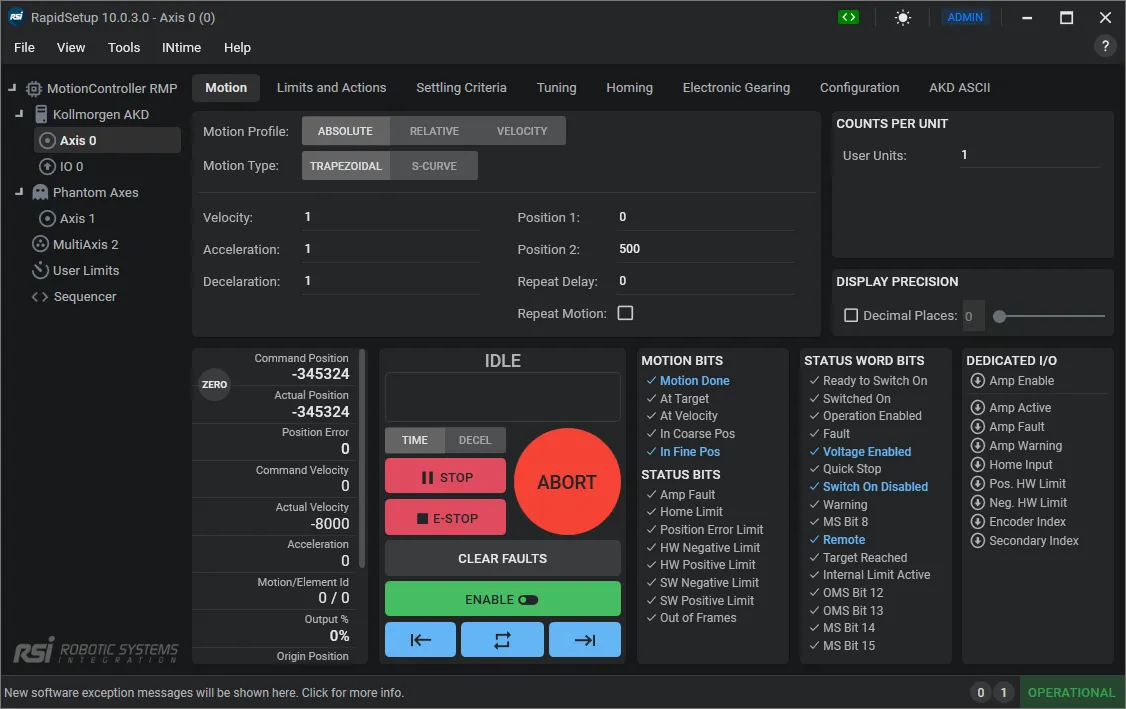
6. Hardware Agnostic
The RMP EtherCAT® supports a wide array of EtherCAT nodes. The OEM can utilize the best servo, stepper, and IO hardware to maximize machine performance.
7. Innovation
RtTasks & RapidCodeRT
OEM can run blocks of user code within the firmware (RTOS). This increases machine performance considerably.
Robotics
OEM can use RMP to add robots to handle machine tending. This way a centralized motion controller is handling all the machine tasks.
RapidAnalytics
OEM can track and analyze machine throughput on machines shipped worldwide. The data can help trigger premaintenance service calls before any axes break down.
start developing today!
1000+ customers have already automated with help of our products and team