Hot Wire Foam Cutting Machine
Expanded Polystyrene (EPS) foam hot wire contour cutting machines use a thin, electrically heated wire to slice through foam blocks, melting the material along a precise path. This technique produces smooth, clean cuts and reduces waste by vaporizing excess foam instead of generating debris. The machines are widely used to create custom foam shapes for packaging, insulation panels, architectural elements, signage, and prototypes in manufacturing and construction. Given the versatility of foam cutting, industries ranging from building construction and sign making to aerospace and theme fabrication rely on these machines.
Axis Configuration of Foam Cutting Machines
EPS foam hot wire contour cutters typically feature a minimum of four motorized axes. These include independent X/Y axes on one tower and Z/W on the other, enabling the hot wire to dynamically tilt and follow complex contours for precise, tapered, or asymmetrical cuts. This dual-tower architecture allows each end of the hot wire to move independently, expanding the range of shapes that can be produced.
Some machines include a fifth rotary axis, such as a turntable, to allow rotational manipulation of the foam block during cutting. This is useful for cylindrical or helical shapes. Others may incorporate additional linear axes for block feeding or automated loading systems. In high-throughput applications, multi-wire configurations are used, allowing multiple identical profiles to be cut simultaneously from a single block, dramatically improving productivity.
The motion control system must synchronize all axes with sub-millisecond precision to prevent distortion in the cut profile, especially during tight curves and transitions. As design complexity increases, the need for smooth, coordinated multi-axis motion becomes critical to maintain accuracy and surface quality.
I/O Requirements for Hot Wire Foam Cutters
- Hot Wire Temperature Control: Maintains consistent heat using analog or PWM outputs for clean cuts.
- Homing, Limit Switches & E-Stops: Ensures safe, repeatable motion and emergency shutdowns.
- Interlocks & Safety Circuits: Prevents operation when safety doors are open or faults occur.
- Wire Tension Monitoring: Enables real-time tension control for accuracy and wire life.
- Auxiliary Outputs: Manages fans, conveyors, and status indicators for machine coordination.
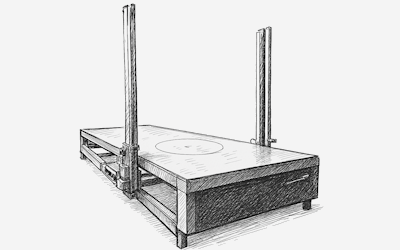
解决方案
Why OEMs Choose the RMP EtherCAT Master and Motion Controller
RSI provides the RMP EtherCAT Master and Motion Controller for precise real-time control. OEMs select RMP for its deterministic performance on both Windows (with INtime RTOS) and Linux (with PREEMPT_RT), ensuring consistent operation. RMP turns any x86 PC into a high-performance motion controller, offering scalability up to 128 axes and thousands of I/O points. Its software-based model allows for modular design, enabling rapid customization and development without proprietary hardware.
Whether running on Windows or Linux, RMP leverages a real-time scheduler to achieve precise EtherCAT cycle rates (500 Hz up to 4–8 kHz) and tight synchronization of all axes. This determinism is crucial – it means the wire moves at constant speed and the control loop never skips, resulting in consistent cut quality even in complex contours.
RMP is a pure software solution that turns an industrial PC into a multi-axis motion controller – no proprietary CNC hardware required beyond a standard NIC port for EtherCAT communication. OEMs can choose any x86-64 PC or even ARM-based IPC (Raspberry Pi 5) that meets their cost and performance needs.
RMP’s G-Code Integration
- Built-in Interpreter: RMP includes a native G-code engine for direct execution, eliminating the need for custom parsers.
- Real-Time Execution: Runs alongside motion control with high-speed contouring and custom M-code support for features like wire temperature adjustment.
- Operator Familiarity: Many users already know G-code from CNC, 3D printing, or routing, reducing training time and increasing productivity.
- Flexible and Parametric: G-code supports macros, variables, and loops, allowing reusable, adaptable cutting routines.
G-code support in RMP gives OEMs a fast, compatible, and powerful way to program and operate foam cutting machines, simplifying development and enhancing user experience.
RMP Motion Features Utilized in Foam Cutting
- Direct G-Code Execution: Interprets and runs G-code natively for complex multi-axis paths without custom code.
- Coordinated Multi-Axis Profiles: Ensures synchronized motion across all axes for precise, tapered, or 3D cuts.
- Motion Blending and Contouring: Allows continuous motion between segments to avoid surface defects and maintain smooth cutting.
- Streaming and Coordinated Motion with External Feeds: Supports real-time trajectory updates, enabling adaptive cutting even on moving materials.
- High-Speed Position Capture and Registration: Captures axis positions instantly based on sensor triggers for precise alignment.
RMP I/O Features and Integration
- Real-Time I/O Synchronization: Tie digital or analog I/O actions to motion events or conditions, such as wire temperature control or tension threshold handling.
- RTTasks for Machine Logic: Use RTTasks to build real-time logic for operations like homing sequences, gantry synchronization monitoring, and motion-activated routines without a separate PLC.
- Deterministic I/O Performance: Inputs are read and outputs updated every servo cycle (e.g., every 1 ms), enabling precise reaction times. The sample rate can be increased and relies on the CPU power.
- Scalability: Handle up to 10,000+ digital and analog I/O signals across distributed devices with consistent timing.
- Safety over EtherCAT (FSoE): Seamlessly integrate E-stops and interlocks into the EtherCAT network with safety-certified timing and reduced wiring.
RMP unifies motion control and I/O management in a single real-time PC-based platform. This allows OEMs to simplify architecture, eliminate separate PLCs, and build reliable, responsive machines with ease.
Vision and AI – An Emerging Opportunity for PC-Based Control
- Automated Inspection: Integrated cameras verify foam dimensions and cut quality, reducing defects.
- Smart Cut Verification: Vision systems scan and align foam blocks pre-cut to adjust toolpaths automatically.
- Predictive Maintenance: AI monitors signals like wire current and motor torque to detect wear and prevent downtime.
- Unified Processing: RMP's PC-based architecture allows vision and AI tools to run alongside real-time control, simplifying integration.
- Flexible Integration: Open architecture supports USB/GigE cameras, OpenCV, and AI libraries like TensorFlow for fast deployment.
RMP's platform allows OEMs to future-proof their machines by integrating vision and AI for smarter, more adaptive foam cutting systems. OpenCV is an open-source option pursued by some machine builders.
Conclusion
This unified control system ensures tight coordination between motion, logic, and user interaction, and allows OEMs to adapt quickly to market changes or customer-specific needs. With strong support and extensible architecture, RMP continues to evolve with emerging technologies, securing its place as a reliable platform for modern machine control.