Case Study
Automated Optical Inspection (AOI)
Automated Optical Inspection (AOI) machines are crucial in electronics manufacturing, used to inspect assembled printed circuit boards (PCBs)for defects. Using high-resolution cameras and sophisticated image processing, these systems verify component placement, presence, and soldering accuracy. There are two types of AOI systems. The 2D AOI employs cameras capturing top-down and sometimes angled views, evaluating component presence, polarity, and solder joints. Meanwhile, the 3D AOI incorporates height measurements through structured light or stereoscopic imaging to evaluate solder volume and component height, greatly improving defect detection reliability.
Modern AOI machines typically integrate both methods to minimize false positives while maximizing detection accuracy.
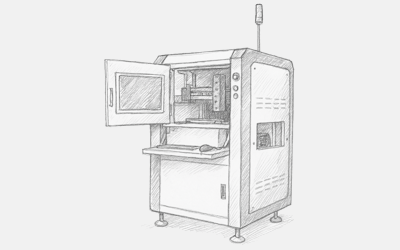
Solution
Motion System and Axes
At RSI, we understand the critical role of motion control in Automated Optical Inspection (AOI) systems, particularly for accurate camera positioning and synchronized image capture. Typical motion axes managed in AOI systems include:
- X-Axis: Movement along the width of the PCB (typically the horizontal direction in the machine frame).
- Y-Axis: Movement along the length of the PCB (perpendicular to the X-axis), enabling full scanning coverage when combined with X motion.
- Z-Axis: Vertical adjustments for focus and height compensation.
- Theta/Tilt Axis (optional): Angled camera views to inspect solder joints effectively.
- Conveyor Axis: Automated PCB transport.
- Board Stop/Clamp: Secures PCB position during inspection.
High-performance AOI typically involves coordinated multi-axis motion to achieve detailed and precise inspections.
Customer utilized stop-and-go and continuous scanning approaches using RMP EtherCAT Motion Controller:
Stop-and-Go Scanning:
In this approach, the customer programmed the RMP EtherCAT motion controller to move and halt the camera precisely at predetermined inspection points. Leveraging RMP's Point-to-Point motion capabilities, they achieved exact positioning with minimal overshoot and vibration. This allowed for stable, repeatable camera alignment in a closed-loop system, ideal for fixed-point image capture in AOI processes.
Continuous Scanning:
For continuous scanning, the customer utilized RMP’s advanced multi-axis streaming coordination features, including PT, PVT, or PVTAJ motion types, to enable uninterrupted, smooth camera motion. This ensured precise synchronization between the camera's continuous movement and the timing of image captures. Additionally, the customer took advantage of the RMP Path Motion feature available within the Cartesian Robot class to streamline complex continuous scanning trajectories.
Why the Customer Chose RMP EtherCAT Master and Motion Controller Over PLC — and Its Standout Motion Programming Features
The customer selected the RMP EtherCAT motion controller instead of a traditional PLC to meet its advanced automation needs. They cited RMP’s superior real-time control, precise motion coordination, and flexible integration capabilities. Recognizing the limitations of PLCs, particularly their reliance on rigid ladder logic and basic motion control, the customer opted for RMP to implement sophisticated multi-axis trajectory planning methods such as PT, PVT, PVTAJ, and Point-to-Point. These features proved ideal for the company’s high-speed, high-precision application.
The RMP platform's software-based, PC-driven architecture simplified the integration of vision system, user interface, and complex logic within a single industrial PC. This eliminated the need for additional controllers, reducing development time and system complexity. The use of the EtherCAT network further enhanced scalability and minimized wiring, allowing the OEM to adapt quickly to changing inspection demands.
RMP’s advantages extend deeply into motion programming and system integration:
- Cross-Platform Support: The developers chose between Windows or Linux environments based on application needs—without compromising real-time performance.
- RapidCode API: With support for C++, C#, VB.NET, and Python, the unified API enabled developer to build advanced machine logic using object-oriented constructs like Axis, MultiAxis, and IO. The API support to subscribing to input events using callbacks or polling, allowed responsive interaction with IOs.
- High-Speed Motion Updates: With servo loop rates typically at 1 kHz or higher, the system delivered millisecond-level updates for motion and I/O. This ensured smooth path transitions, accurate triggering, and reduced vibration.
- Motion Safety and Constraints: Built-in safety features included software-defined travel limits, following error protection, and integration with drive-level safety (e.g., Safe Torque Off). These safeguards helped protect sensitive optics and electronics.
- Safety over EtherCAT (FSoE): RMP supports Functional Safety over EtherCAT (FSoE), that enabled safety-critical data to be transmitted over the same EtherCAT network. This reduced wiring complexity and simplified safety system design while meeting stringent SIL standards.
- Data Logging and Tuning: Tools like RapidScope allowed for real-time data capture and PID tuning to refine performance. The suer could record all the data by leveraging Recorders feature.
- Vision System Integration: Running on standard operating systems, RMP seamlessly interfaced with popular vision libraries and AI tools. The developer could coordinate motion and imaging via multithreaded execution, shared memory, or remote interfaces.
Testimonial
Technologies
Benefits
Images
Additional
On this page