Case Study
Robotic Surgical Systems
Robotic guided surgery is a form of minimally invasive surgery where surgeons operate through robotic instruments, achieving enhanced precision and control. These systems translate surgeons' hand movements into precise, sub-millimeter instrument motions, significantly reducing tissue trauma and improving patient outcomes. Achieving this precision demands an advanced motion control solution, as even slight latency or jitter can compromise surgical accuracy and safety.
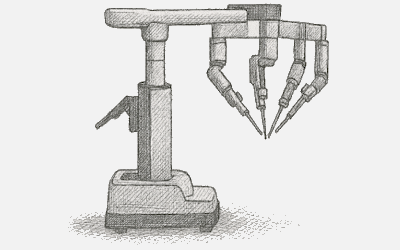
Solution
Axis Count and Motion
Modern robotic surgical systems typically involve multiple robotic arms, each providing around seven axes of movement, similar to a human arm and wrist. A system could have several robotic manipulators to precisely position surgical instruments and cameras. This axis count is comfortably managed by the RMP controller, supporting up to 128 synchronized motors.
Each robotic arm’s axes contribute uniquely: initial joints handle broad positioning over the patient, while distal and wrist axes enable fine dexterity within the surgical site. The RMP Master and Motion Controller coordinates these axes in real time, utilizing streaming trajectories to smoothly translate surgeon commands into precise, coordinated movements. The result is precise motion of the instruments, with no jerks or overshoot, which is essential for delicate surgical tasks.
I/O Requirements (Sensors, Actuators, and Safety)
Robotic surgical systems have extensive I/O requirements, integrating numerous sensors, actuators, and critical safety signals. Our design incorporates EtherCAT modules for digital inputs (limit switches, home sensors, foot pedals, buttons) and digital outputs (indicator lights, brakes), as well as analog inputs (force/torque sensors) for precise force feedback control, providing surgeons enhanced situational awareness through tactile feedback.
The system handles hundreds of I/O signals in real-time alongside motion control, taking advantage of the RMP controller’s capability to manage over 10,000 digital and analog I/O points on a single EtherCAT network. Real-time deterministic I/O triggers synchronize external actions, such as activating surgical tools or capturing images, precisely with robot movements.
Safety is integrated through Functional Safety over EtherCAT (FSoE), enabling safety-rated inputs (emergency stops, interlocks) and outputs (servo drive STO) to operate securely within the same EtherCAT network. Utilizing a Beckhoff TwinSAFE safety controller, the solution meets SIL3/PLe safety standards without requiring additional hardware or wiring, significantly simplifying the system architecture while ensuring rapid, networked safety responses.
RMP Motion Features Utilized (Streaming & Real-Time Control)
A core technical enabler is the RMP’s integrated motion control engine, specifically its Streaming Motion and RTTasks features. Together, these features enable real-time, surgeon-driven control with ultra-smooth, deterministic behavior across all robot axes.
With Streaming Motion, our system continuously feeds trajectory points—captured from joystick and foot pedal inputs—to RMP at 1–4 kHz using formats like PT and PVT. This allowed precise, multi-axis tool control that feels immediate and natural, even during fast or unpredictable surgical maneuvers.
Customers can also use on-the-fly trajectory modification, essential for dynamic adjustments. For example, if the system detects unexpected force feedback or approached soft travel limits, the user can instantly decelerate or redirect the tool path—providing a crucial safety layer beyond passive hardware stops.
To tie motion, IO, and feedback together, customers can utilize RMP’s RTTasks. This allows high-priority, real-time threads that synchronize directly with the motion cycle. RTTasks can ran within a few microseconds, handling tasks like:
- Reading joystick and pedal inputs
- Streaming new trajectory points
- Monitoring sensor data (e.g., force thresholds)
- Logging real-time metrics (position, torque, etc.)
- Responding instantly to limit switches or safety triggers
The control loop maintains microsecond-level determinism—even under load. This tight integration ensures that motion commands, I/O responses, and process monitoring are all executed in lockstep with each motion cycle.
The result is a robot that truly felt like an extension of the surgeon’s hands, with built-in adaptability and safety for the surgical environment.
RMP I/O Features Utilized (Safety over EtherCAT and More)
RMP’s I/O and safety capabilities are essential to build a responsive, real-time surgical robot. Users can implement Functional Safety over EtherCAT (FSoE) with Beckhoff TwinSAFE, enabling synchronized E-stops and STO signals across all axes within a 4 ms cycle—without additional wiring. RMP handles both safety and control traffic on a single EtherCAT network, simplifying design while meeting SIL3/PLe standards.
For runtime protection, users can leverage RTTasks to monitor joint positions and issue immediate halt commands if soft limits were approached. RTTasks also triggers precisely timed outputs—like camera captures—synchronized to motion cycles with millisecond accuracy.
RMP’s support for dedicated motion I/O (limit switches, home sensors, drive faults) makes homing and fault handling seamless. Customer can use the Capture feature for microsecond-accurate encoder latching during calibration.
With broad EtherCAT compatibility, RMP easily integrates devices from Beckhoff, Elmo, and others—giving users a unified, deterministic architecture where motion, I/O, and safety worked together in real time.
Vision and AI Integration for Future Innovation
One major advantage of using RMP on a PC-based platform is its readiness for integrating vision and AI technologies. As surgical robotics evolves, features like camera-based guidance, AI-driven safety checks, and autonomous assistance will become essential. Our Linux-based RMP system makes this easy—vision data from cameras can be processed in real time, and results can feed directly into the motion controller via shared memory or RMP’s gRPC API.
For instance, a stereo camera could track anatomy in real time, sending micro-corrections to RMP to adjust tool paths on the fly—something difficult to achieve with PLCs. Python-based AI models can even interface directly with RMP using RapidCode, allowing real-time behavior adjustments without complex middleware.
RMP’s PC-native design enables us to blend motion control, vision, and AI on a single platform.
Conclusion
Building a robotic surgery system demands precision, safety, and adaptability—and RMP on Linux delivered across the board. With deterministic multi-axis motion, integrated safety over EtherCAT, and real-time performance using PREEMPT_RT, these systems can achieve surgeon-level responsiveness and reliability.
RMP’s PC-based architecture gives customers the flexibility to interface with high-level software, plan for future AI/vision features, and scale the system from 4 to 40+ axes—all while keeping costs in check. RTTasks enabled microsecond-level reaction time, and the unified EtherCAT network simplified design and reduced hardware.
Testimonial
Technologies
Benefits
Images
Additional
On this page