Case Study
Wafer Bonding System
Introduction to Wafer Bonding Systems
Wafer bonding plays a vital role in semiconductor device manufacturing by permanently joining two aligned wafers. It supports key applications such as wafer-level packaging, 3D stacking, and fabrication of specialized substrates like SOI. Executing it with precision requires careful control of parameters like force, heat, and vacuum.
OEMs building wafer bonding systems face common automation challenges: multiple motion axes for wafer handling and alignment, numerous I/O signals for vacuum and safety, and a need for high precision. This case study details how our customers have addressed these challenges using RMP EtherCAT Master & Motion Controller.
Multi-Axis Motion in Wafer Bonding Machines
Our customers have varying machine designs, but typical wafer bonding systems are multi-axis machines. A representative design includes about six motion axes: an X–Y stage plus a rotary θ axis for alignment, a Z axis for bringing wafers together under force, and an axis for wafer handling (e.g., robotic arm or linear slide for loading/unloading wafers). Some tools add more axes for multiple bond stations or conveyors.
During alignment, the X, Y, and θ axes move in a coordinated fashion to achieve micron-level accuracy. Then, the Z axis drives the wafers together smoothly to avoid misalignment. This process requires tightly synchronized multi-axis motion and advanced trajectory control.
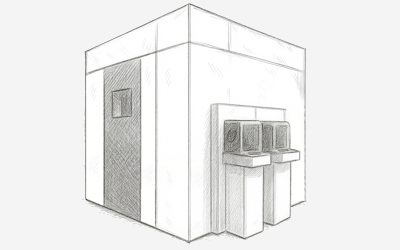
Solution
I/O Requirements: Sensors, Valves, and Safety Interlocks
Our customers need to integrate dozens to hundreds of digital and analog I/O points. These include:
- Digital outputs to actuate vacuum valves and chamber pumps
- Analog inputs to monitor pressure sensors for vacuum level confirmation
- Temperature controller inputs for heating elements
- Digital I/O for high-voltage bonding triggers and UV lamp activation
- Safety inputs from interlocked doors and light curtains
Safety signals such as emergency stops and torque-off interlocks are often integrated via Safety-over-EtherCAT (FSoE) to meet SIL safety standards. OEMs require deterministic timing between I/O and motion, such as activating vacuum precisely when the chuck touches the wafer or capturing sensor data on motion events, benefit from using RTTasks.
Why OEMs Choose a PC-Based EtherCAT Motion Controller
OEMs have evaluated traditional PLCs, but ultimately chose a PC-based solution: the RMP EtherCAT Master & Motion Controller. Key benefits include:
- Unified Controller and HMI: RMP firmware runs on a dedicated real-time OS core (Windows + INtime RTOS or Linux + PREEMPT_RT), while GUI and analytics operate on other cores. This setup enables real-time control with a familiar software environment.
- EtherCAT and Modular I/O: The built-in EtherCAT master enables direct PC communication to all drives and I/O modules. OEMs benefit from simplified wiring and extensive device compatibility (100+ supported EtherCAT devices).
- Scalability: RMP supports up to 128 coordinated axes and over 10,000 I/O points. OEMs can easily expand their systems without changing controllers.
- Real-Time Performance: Servo loops run at 1 kHz or higher with microsecond-level jitter. OEMs confirm repeatable motion and I/O timing essential for bonding precision.
- Integration Flexibility: RMP supports C++, C#, Python, and gRPC APIs. OEMs easily integrate vision libraries, data logging, and advanced features without proprietary scripting.
Motion Control Features Used by OEMs
- Coordinated Multi-Axis Moves: Grouping X, Y, θ for alignment and synchronized motion.
- Trajectory Streaming (PT, PVT, PVTAJ): Custom profiles for Z-axis approach and smooth wafer contact.
- On-the-Fly Trajectory Modify: Adjust alignment based on real-time sensor or vision input.
- Position Capture: Latch encoder positions from touch sensors for bond force consistency.
- Gantry and Electronic Gearing: Maintain squareness on dual Y-axis gantries and synchronize auxiliary axes.
- Virtual (Phantom) Axes: Simulate and test multi-axis motion sequences prior to hardware availability.
I/O and EtherCAT Features Used by OEMs
- Deterministic I/O Triggering: Output signals tied to precise motion positions or cycle counts.
- Integrated Digital/Analog I/O: Unified I/O handling for limits, interlocks, temperature, and vacuum.
- High I/O Counts and EtherCAT Expansion: Seamless integration of new sensors and modules across vendors.
- Safety-over-EtherCAT (FSoE): Enables safe torque-off and e-stop handling in software.
- High-Speed Data Logging: Capture position, force, and I/O traces during development.
Future Innovations: Vision and AI
PC-based control gives OEMs an advantage in integrating machine vision and AI tools. Examples include:
- OpenCV Integration: Vision-guided alignment routines adjust motion in real-time.
- Machine Learning: Bond force and pressure data are used to train models for process optimization.
- ROS 2 Compatibility: PC-based controllers can interface with ROS for simulation and higher-level orchestration.
RMP’s support for standard APIs, real-time Linux (using PREEMPT_RT) and Windows (using INtime), and modern development environments enables advanced use cases like predictive maintenance, visual servoing, and autonomous adjustment loops.
Conclusion
OEMs building wafer bonding systems have increasingly adopted the RMP EtherCAT Motion Controller for its performance, scalability, and integration capabilities. It offers a single PC-based platform for motion, I/O, safety, and software applications enabling rapid development and high-precision control.
Testimonial
Technologies
Benefits
Images
Additional
On this page